Abrasive Sandblasting
Abrasive sandblasting is a process used to clean and smooth surfaces, typically metal, by propelling tiny particles of an abrasive material against its surface at high speeds. This method has many industrial applications such as removing rust or paint from metal, smoothing masonry or stone surfaces, and creating a textured finish on materials like glass. It is a quick and effective way to prepare surfaces for further work or treatment.
​
Using abrasive sandblasting requires the use of special equipment including an air compressor, blasting nozzle and an abrasive material such as silica sand or crushed glass. The compressed air forces the media through the nozzle at high speed while the operator holds it close to the surface being treated in order to effectively remove contaminants. Safety precautions should always be taken when using this type of machinery due to its potential for causing injury if not operated properly.
​
Here at Signature Blasting Services, we carry an extensive inventory of abrasive sandblasting equipment to support in-situ turbine maintenance anywhere in North America. Our specialized crew has extensive experience with a variety of grit blasting services including aluminum oxide, glass bead, steel shot as well as CO2 (dry ice) blasting, and can help meet a wide range of OEM specifications.
​
For example, for steam turbines, adherent oxide deposits may form in the steam flow path, distorting the original shape of turbine nozzles and blades. These deposits are often rough and uneven at the surface, increasing both high and low pressure steam flow resistance. Distortion of steam passages alters steam velocities and pressure drops, reducing the capacity and thermal efficiency of the steam turbine, ultimately impacting the business bottom line. If conditions worsen further, there is potential for the deposits to cause excessive rotor thrust; where uneven deposition can impact the balancing of turbine rotor, causing vibration challenges leading to major asset damage.
Similarly, for gas turbines, power augmentation and extended time on turning gear can add to the risk of rust and other deposits accumulating in the rotor slots. Often, because of accumulation, removing all the blades can be a challenging evolution, as can be reinstalling the blades, besides the inherent schedule and cost impact on maintenance outages.
Removing insoluble scales and deposits from the turbine blades and auxiliary components through blast cleaning allows optimum thermal performance efficiency and equipment reliability. Additionally, blasting technologies offered by Signature Blasting Services helps provides optimal cleaning to facilitate high integrity NDE/NDT inspection to support long term asset reliability and life cycle management plans of your gas and steam turbine systems.
​
Grit Blasting Services
Grit blasting services are a specialized form of abrasive blasting used to clean and prepare surfaces for coating or to remove existing coatings. It is done by combining pressurized air and small particles of an abrasive material travelling at high velocity in order to clean, polish, deburr and roughen the surface. Grit blasting services are commonly used in automotive, aerospace and manufacturing industries, as well as other industrial applications.
​
Our on-site grit blasting services are performed right on the turbine deck, often in-situ, eliminating the expenses associated with shipping components off-site or to the manufacturer, providing essential cost savings and schedule and efficiencies to our partners. All work is performed using dust containment systems that eliminate nuisance dust and debris, and also help minimize dry waste debris.
Signature Blasting provides grit blasting services that are specially geared towards some of the following turbine parts and components:
​
-
Rotors
-
Disc and Blade Rings
-
Trunnions and Journal Bearings
-
Stop/Throttle/Steam Valve Components (stem and bushings)
-
Inner, Outer, and Fixed Lower Casings
-
Studs, Nuts, and Washers
-
Generator Stator and Windings
Our expert team at Signature Blasting Services will work closely with our customer partners to determine the specifics of the technology based on a wide variety of factors including application, material, OEM specifications, regional regulations, regulatory requirements, budget, and schedule.
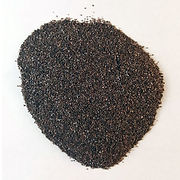
Aluminum Oxide Sandblasting
Aluminum Oxide Sandblasting is an efficient and cost-effective method for surface abrasion. It is a common process used in metalworking and automotive industries, as well as for decorative applications. This abrasive sandblasting technique uses finely ground aluminum oxide particles propelled through pressurized air to remove paint, rust, and grime from surfaces. The result is a pristine surface ready for painting or other finishing work.
​
Aluminum Oxide Sandblasting provides several advantages due to its hardness and durability. It can effectively remove heavy layers of paint without damaging the underlying material because it produces very little dust or heat buildup during the sandblasting process. Additionally, it is non-toxic and suitable for use on both ferrous and non-ferrous metals.
​
Due to its high etch properties and its fast working speeds, aluminum oxide is an extremely popular media for blast cleaning. Because of its high purity rating (90% and up) and consistent grit size, aluminum oxide can also be recycled multiple times, which not only makes it more environmentally friendly, but also provides a sizeable cost advantage. Additionally, aluminum oxide contains significantly less silica than other media such as sand, typically less than 0.3%, and is an inherently safer option as well.
​
Aluminum oxide sandblasting uses a harder compound than most other commonly used blasting materials such as glass or plastic grit and is often one of the first choices when needing to remove unwanted deposits and coatings from even the hardest metal surfaces. Its versatility and strength make it also makes a great option for coating removal and surface preparation in advance of a new coating or paint being applied. It is widely used in abrasive sandblasting not only due to this cost advantage but also because of its longevity.

Black Beauty®
The Black Beauty® line of abrasives is a coal slag abrasive material ideal for use in the removal of paint, scale, and rust from metal surfaces, and prepping surfaces for coating application.
It is also classified as “low free silica”, containing less than 0.1% free silica, and hence a preferred alternative to silica sand. It is also chemically inert and almost entirely recyclable. It provides enhanced cutting performance relative to traditional abrasive media, and helps attain a high level of control during application due to its uniform density and grading. It is also moisture-free and repels water, minimizing the risk of rusting and dampness.
Additionally, Black Beauty® meets a wide range of industry abrasives specifications and environmental standards including California Tile 17 (CARB), SSPC AB1, MIL-A-22262B (SH), and 40CFR 261.24a (TCLP). It is generally available in three standard grades – medium, fine, and extra fine, which can be catered for the specific application.

Steel Shot
Steel shot blasting technique is the most widely used method for shot peening applications, but also finds extended usage in metal surface preparation such as cleaning, stripping, and polishing. Steel shot blasting is available in a variety of sizes but is always designed in spherical shapes. The shape produces a clean, smooth, and polished surface on the target material through a peening action created by the acceleration of the steel shot. Shot peening hardens the surface of a metal being blasted by the repeated striking of the surface with steel shots. This repeated striking imparts compressive residual stresses on the surface with microscopic plastic deformation that helps increase its surface hardness and material strength, and protects high duty assets against fatigue and cracking.
For cleaning and surface treatment applications, the grade or size of the steel shot will determine the ultimate finish achieved on the surface of the metal. For example, smaller steel shots typically result in a smoother and more polished surface, whereas larger shots will clean more aggressively but produce a coarser surface finish.
Since steel shot does not use an abrasive process and the media does not easily break down, only a minimal amount of dust is created in the blasting process. Steel shot also offers an impressive number of use cycles before needing replacement – as many as 150 to 200 cycles, depending upon the application and the use of blast media recovery equipment.
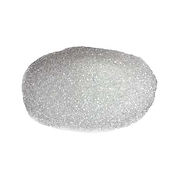
Glass Bead
Glass bead blasting is an effective method for cleaning surfaces without leaving behind much of a blast profile. This makes it ideal for paint or coatings removal, sheen surface finishing, polishing, metal cleaning, as well as rust remediation and foreign material removal. If a profile is desired, a blast media such as steel shot or aluminum oxide sandblasting is recommended instead.
​
Additional benefits of glass bead blasting include its chemical inert characteristic as well as its recyclability. It is not uncommon for glass bead media to last 4 – 6 cycles before needing replacement. During the blasting cycle, the deposits, which have been dislodged by the action of the glass beads, are typically removed by filtration of the glass beads and debris together. The glass beads which have been broken during the operation are also removed at this stage of the filtration, thus ensuring that only perfectly round beads are recycled, minimizing the risk of any undesired abrasion.
​
Glass bead blast media comes in a variety of sizes ranging from 40 – 325 mesh sizes. The fastest cleaning glass bead is typically 60-100 mesh. Ultimately, the right size blast media will depend on your specific application.
​
For example, finer glass beads are better suited for creating a very smooth surface finish often with a satin-matte finish. Medium-size glass beads are a more suitable choice when working with metals and alloys such as aluminum and stainless steel, ideal for evening out imperfections like scratches and machining marks. Larger size glass beads work well for cleaning and light deburring of rough surfaces, such as those found on cast metal.